Discover essential insights on bagging machine prices in Australia. Get tips on costs, financing options, and key considerations to make an informed purchase.
Key Takeaways
- Bagging machine prices in Australia range from $10,000 to over $150,000, depending on automation level, capacity, and features.
- Types include manual, semi-automatic, and fully automated bagging machines, suitable for different industries and production scales.
- Operating costs include energy consumption, maintenance, and spare parts, impacting long-term investment value.
- Government incentives, leasing, and business loans are available financing options to offset upfront costs.
- Compliance with Australian standards (ISO, HACCP, NMI certification) is essential for food, pharmaceutical, and trade applications.
Bagging machines are essential for streamlining packaging operations in industries like food production, agriculture, pharmaceuticals, and construction. These machines increase efficiency, reduce labour costs, and enhance product consistency. Whether you need an entry-level unit for small-scale operations or a high-speed, fully automated system, understanding the costs, machine types, compliance, and financing options will help you make the right investment.
This guide covers everything you need to know about purchasing a bagging machine in Australia, including types, prices, maintenance, warranties, compliance, financing, and common mistakes to avoid.
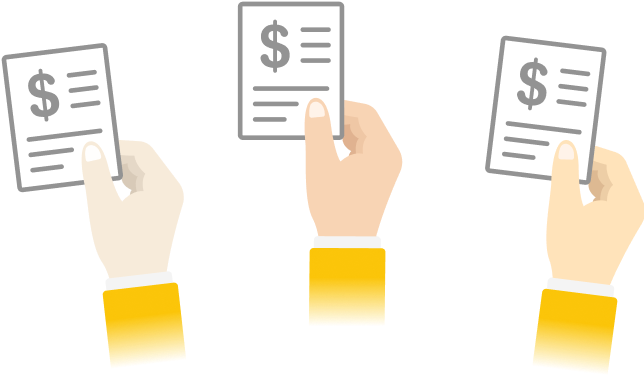
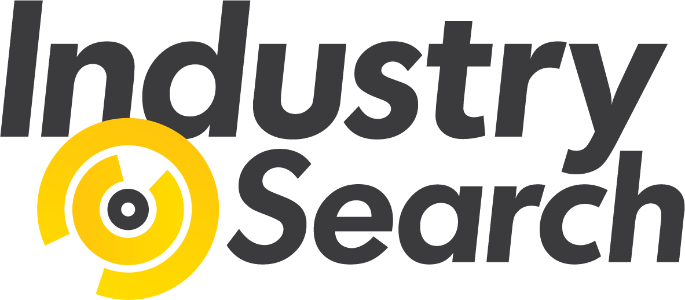
Find the right Bagging Machine
Compare quotes from expert Australian suppliers and make the best choice. It's free, quick and easy!
Types of Bagging Machines
Bagging machines come in various configurations to suit different applications and industries:
1. Manual Bagging Machines
- Require human intervention for loading, sealing, and weighing bags.
- Ideal for low-volume operations.
- Cost: Starts from $10,000 to $30,000.
2. Semi-Automatic Bagging Machines
- Operators manually place bags, but weighing, filling, and sealing are automated.
- Suitable for small to medium production lines.
- Cost: Ranges from $30,000 to $80,000.
3. Fully Automatic Bagging Machines
- Fully automated bag placement, weighing, filling, sealing, and palletising.
- Best for high-speed, large-scale operations.
- Cost: From $80,000 to over $150,000.
4. Industry-Specific Bagging Machines
- Valve Bag Fillers: Used for cement, flour, and powdered products.
- Form-Fill-Seal Machines: Create, fill, and seal bags from roll stock, common in food and pharmaceutical packaging.
- Vacuum Bagging Machines: Extend shelf life for perishable goods like meat and dairy.
Bagging Machine Prices in Australia
Bagging machine prices vary based on machine type, speed, and level of automation. Here’s a breakdown of the cost range and best applications for each type:
- Manual Bagging Machines ($10,000 – $30,000): Ideal for small businesses and low-volume packaging, requiring manual intervention for bag placement and sealing.
- Semi-Automatic Bagging Machines ($30,000 – $80,000): Suitable for medium-sized businesses, offering improved efficiency by automating some processes like weighing and sealing.
- Fully Automatic Bagging Machines ($80,000 – $150,000+): Best for large-scale, high-speed production, where automation handles bag placement, filling, sealing, and palletising.
- Industry-Specific Machines ($50,000 – $200,000): Designed for specialised applications in industries like food, pharmaceuticals, and construction (e.g., valve bag fillers for cement, vacuum baggers for food packaging).
Selecting the right machine depends on production volume, budget, and industry-specific requirements.
Operating Costs, Maintenance & Spare Parts
The ongoing costs of a bagging machine include energy consumption, material usage, and maintenance. Machines typically use 5–20 kWh of electricity, and some require compressed air, adding to operational expenses. The choice of bagging materials—pre-made bags or roll stock—also impacts costs.
Regular maintenance is crucial to ensure efficiency and longevity:
- Daily cleaning prevents material build-up and ensures smooth operation.
- Monthly calibration maintains accurate bag weights.
- Annual servicing is necessary for motors, weighing sensors, and sealing components.
Spare parts can be a significant cost, with common replacements including:
- Sealing elements (heat seal bars, ultrasonic sealers): $500–$3,000
- Weighing load cells: $1,500–$5,000
- Motors & belts: $2,000–$10,000
Proper maintenance and timely part replacements help minimise downtime and unexpected costs, ensuring long-term reliability.
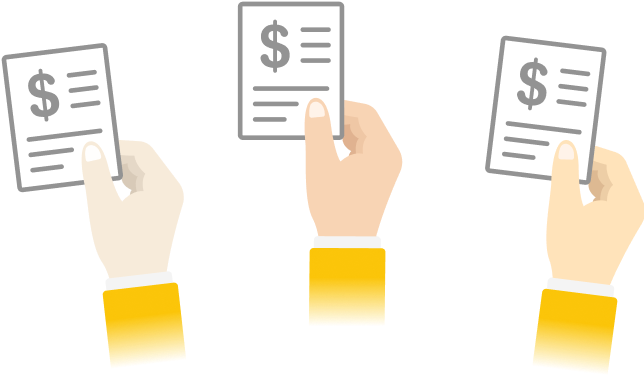
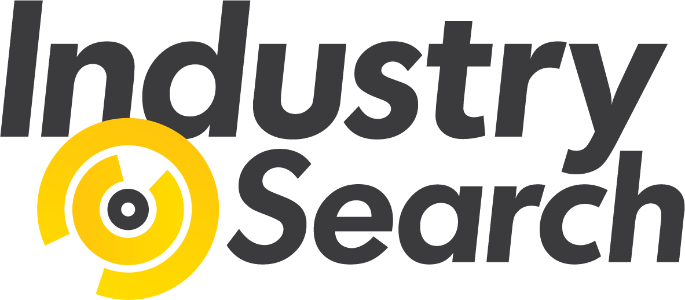
Find the right Bagging Machine
Compare quotes from expert Australian suppliers and make the best choice. It's free, quick and easy!
Financing Considerations
Investing in a bagging machine is a major capital expense, but several financing options can make it more affordable:
- Leasing – Spread payments over time without a large upfront cost. Leasing agreements typically have interest rates between 5–8%, with options to upgrade or purchase at the end of the term.
- Hire Purchase – Own the machine after making fixed payments over 2–5 years, often with interest rates ranging from 5–7%. This option suits businesses looking for long-term ownership without a lump-sum purchase.
- Business Loans – Equipment financing loans from banks and lenders generally have interest rates of 5–8%, with flexible repayment terms.
- Government Grants & Tax Incentives – Eligible businesses may benefit from initiatives like the Instant Asset Write-Off scheme, allowing deductions of up to $150,000 for equipment purchases, helping to offset costs.
Warranty & Service Contracts
Protecting your investment with a warranty and service plan ensures long-term reliability and minimises unexpected expenses.
- Standard Warranty – Typically 1–2 years, covering defective parts and manufacturer faults.
- Extended Warranty – Some suppliers offer up to 5 years of coverage, often including critical components like control panels, weighing sensors, and motors.
- Service Contracts – These provide scheduled servicing, priority repairs, and reduced costs for parts and labour, ensuring minimal downtime and prolonged machine life.
Choosing the right financing and warranty package helps reduce financial strain, protect against costly repairs, and maximise the lifespan of your bagging machine.
Compliance & Certification Requirements in Australia
When purchasing a bagging machine in Australia, it’s essential to ensure compliance with industry regulations and safety standards. Non-compliance can lead to operational delays, legal penalties, and product recalls. Key regulatory considerations include:
Industry Compliance & Certification
- ISO 9001 – This internationally recognised standard ensures that the bagging machine is manufactured with strict quality management systems in place, promoting consistency and reliability.
- National Measurement Institute (NMI) Approval – If your bagging machine is used for trade and involves weight verification, it must be NMI-approved to meet Australia’s legal trade measurement requirements.
- Food Safety & HACCP Compliance – Machines used for food, beverage, and pharmaceutical packaging must comply with HACCP (Hazard Analysis and Critical Control Points) standards and Food Standards Australia New Zealand (FSANZ) regulations to ensure hygiene and contamination control.
- TGA Compliance – If bagging pharmaceutical or medical products, your machine may need Therapeutic Goods Administration (TGA) approval to meet strict safety and labelling standards.
- Environmental Regulations – Some machines must comply with energy efficiency and emissions standards under Australian sustainability and waste reduction policies.
Workplace Health & Safety (WHS) & Operator Requirements
- Safety Training – Operators must undergo Workplace Health & Safety (WHS) training to handle bagging machines safely and minimise the risk of workplace accidents.
- Automation Level & Technical Expertise – Fully automated systems require skilled technicians for operation and troubleshooting, while manual and semi-automatic machines require proper training to avoid operational errors.
- Lockout/Tagout (LOTO) Procedures – To ensure worker safety, bagging machines must have proper lockout/tagout systems to prevent accidental startups during maintenance.
By ensuring compliance with these certifications, safety measures, and regulatory requirements, businesses can avoid legal issues, improve operational efficiency, and maintain product integrity.
Installation & Setup Considerations
Proper installation is key to ensuring efficient operation and long-term reliability of bagging machines. Key factors to consider include:
1. Space Requirements & Layout
- Floor Space & Clearance: Bagging machines need sufficient room for operation and maintenance, including space for operator movement, material loading/unloading, and routine maintenance.
- Ceiling Height: Machines like VFFS or bulk fillers may require high ceilings for proper operation.
- Conveyor & Workflow: Ensure smooth integration with existing conveyors and optimise layout to avoid bottlenecks.
2. Integration with Existing Systems
- Weighers & Load Cells: Ensure compatibility with checkweighers and multi-head weighers to maintain product accuracy.
- Conveyors & Material Handling: Ensure seamless connection to automated production lines for optimal product flow.
- Sealing & Labelling: Verify compatibility with sealing and labelling systems for packaging material specifications and compliance.
3. Electrical & Pneumatic Requirements
- Power Supply: Ensure the correct power supply, such as three-phase (415V) or single-phase (240V), based on the machine.
- Compressed Air: Machines using pneumatic components require an adequate air compressor with sufficient pressure and flow.
4. Installation Timeline & Professional Setup
- Lead Times & Delivery: Account for potential delays in delivery for larger or custom machines.
- Professional Installation: Many suppliers offer on-site setup, calibration, and training to ensure proper installation and compliance.
By addressing these considerations, businesses can ensure seamless integration, reduced downtime, and optimised machine performance.
Resale Value, Upgradability, ROI & Cost Savings
When considering a bagging machine, it's essential to assess both its resale value and potential return on investment (ROI).
Depreciation & Resale Value
- Depreciation Rate: Bagging machines typically lose 20-40% of their value over five years, depending on factors like model, usage, and maintenance.
- Upgradability: Many machines allow for modular upgrades to enhance performance and adapt to evolving business needs, which can help retain value longer.
Return on Investment (ROI) & Cost Savings
- Labour Reduction: Automating the bagging process can reduce manual labour costs by 30-50%, improving workforce efficiency.
- Increased Production Speed: A fully automatic bagging machine can process over 1,000 bags per hour, while manual systems only manage 100-300 bags per hour, boosting productivity.
- Material Efficiency: Switching to roll stock instead of pre-made bags can save up to 40% on packaging costs, improving overall material efficiency and reducing waste.
By considering depreciation, upgradability, and the potential ROI from labour savings, faster production, and material efficiency, businesses can make informed purchasing decisions that support long-term profitability.
Common Questions Bagging Machine Buyers Ask
1. How do I determine the right bagging machine for my business?
- Assess production volume, bag types, and automation level needed.
- Consult a supplier to match your requirements with the best machine.
2. How long does a bagging machine last?
- With proper maintenance, a bagging machine can last 10–15 years.
3. Can a bagging machine handle different materials?
- Some machines handle multiple bag types, but it’s essential to check compatibility before purchasing.
4. What ongoing costs should I consider?
- Spare parts, maintenance, energy usage, and operator training.
5. Do I need an NMI-certified machine?
- If selling products by weight, yes—NMI certification is required for legal trade.
Conclusion
Investing in a bagging machine boosts efficiency, reduces labour, and ensures consistent packaging quality. Carefully evaluate costs, compliance, automation levels, and ROI to select the best machine for your needs.