Improve Packaging with Orbital Pallet Wrapping Machines
Businesses today need efficient packaging solutions, and the orbital pallet wrapping machine is a great option. This machine wraps pallets with stretch film horizontally, which helps keep products secure during shipping.
Not only does it provide better load stability, but it also reduces material waste, making it a smart choice for many companies. This article will examine how these machines work and their advantages over traditional wrapping methods.
How Orbital Pallet Wrapping Machines Work
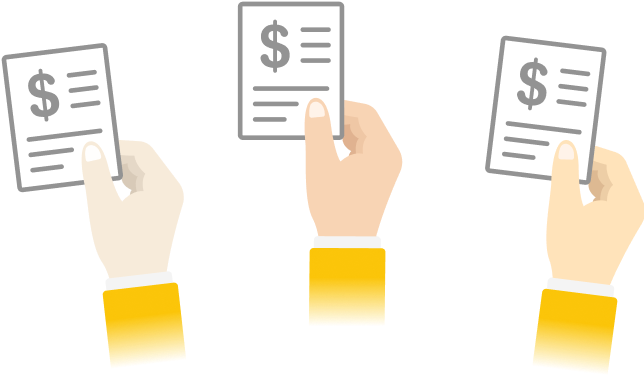
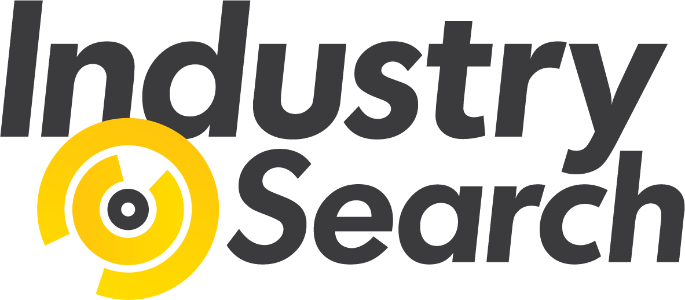
Find the right Orbital Wrapper
Compare quotes from expert Australian suppliers and make the best choice. It's free, quick and easy!
A. Explanation of Orbital Wrapping
Orbital pallet wrapping is a method of securing products on a pallet by wrapping them with stretch film horizontally using an automated machine. Unlike conventional vertical wrapping, where the film is applied from the top to the bottom of a load, orbital wrapping uses a rotating ring that moves around the pallet, applying the film horizontally. This method provides uniform coverage and improved load stability, especially for irregularly shaped items.
B. Horizontal Wrapping Mechanism
All orbital wrapping machines have a rotating ring carrying a stretch film reel. As the ring spins around the product, the reel dispenses the film, securing the load tightly and evenly. The machine can be controlled by various means, including impulse control via a foot pedal, hand pendant, or a programmable logic controller (PLC) for automated control.
Modern orbital wrappers have standard features like dual film reels for better efficiency, automatic film clamping and cutting, and built-in safety measures. These safety features include a fully enclosed ring to protect operators from moving parts and a blade guard to prevent injury during film-cutting. Depending on the model, controls range from simple dial systems to advanced HMI (Human-Machine Interface) touchscreens, making operation user-friendly and parameter adjustments easy.
Step-by-Step Process
-
Loading the Pallet: The pallet is manually loaded or placed on the machine using an integrated conveyor belt (in fully automated systems).
-
Rotation of the Ring: As the pallet remains stationary, the rotating ring spins around the load, applying the stretch film horizontally.
-
Film Application: The machine wraps the film around the pallet in consistent layers until the desired coverage is reached.
-
Completion of the Wrapping Cycle: Once the wrapping cycle finishes, the machine automatically cuts the film, securing the load.
For fully automatic systems, orbital wrappers are integrated with conveyors, enabling a seamless, hands-off process. This automation dramatically increases labour and time savings while reducing the risk of injury.
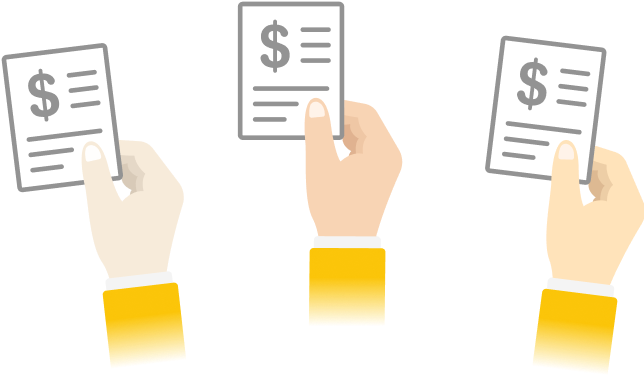
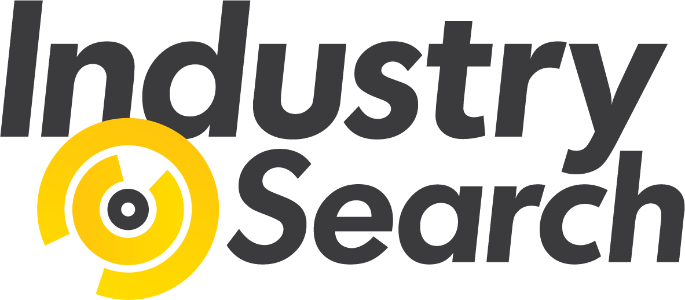
Find the right Orbital Wrapper
Compare quotes from expert Australian suppliers and make the best choice. It's free, quick and easy!
Critical Components of the Machine
-
Rotating Ring or Arm: This component spins around the pallet, applying film as it moves.
-
Stretch Film Reel Carrier: Carries the film reel and dispenses it as the ring rotates.
-
Control Systems: These range from foot pedals and hand pendants to advanced PLCs and HMI touchscreens, and they allow operators to easily adjust speed, tension, and film layers.
-
Conveyor Belt (if automated): Automatically moves pallets in and out of the wrapping area, boosting efficiency.
-
Safety Features: A fully enclosed ring to shield moving parts and a blade guard for safe film cutting are also included.
The process differs slightly in specialised machines, like C-style orbital wrappers. Items such as window frames, rolls of piping, or tyres are placed on a rotating table, allowing the ring to move through the object's centre, ensuring a secure wrap for unconventional shapes.
Advantages of Orbital Pallet Wrapping Over Traditional Methods
1. Improved Load Stability
Orbital wrapping applies consistent tension around the entire load, making it more secure than traditional methods. This helps prevent load shifting during transport, reducing the risk of damaged products.
2. Reduced Material Waste
Orbital wrapping uses less stretch film by applying the exact amount needed, which cuts down on waste. Machines often use pre-stretched film, which is thinner and stronger, providing better results with less material than manual or conventional wrapping.
3. Time and Labor Savings
Automation significantly reduces the need for manual labour. Workers don’t have to wrap loads by hand, and the machine wraps much faster than manual or semi-automatic methods, speeding up the packaging process.
4. Cost Efficiency
Though orbital wrappers require an upfront investment, they offer long-term savings. Businesses save on film, reduce labour costs, and lower the risk of damaged goods, which can lead to a quick return on investment (ROI) over time.
Other Key Benefits for Businesses
1. Consistency and Precision
Orbital pallet wrapping machines provide uniform wrapping every time, ensuring that products are securely wrapped, reducing the risk of damage during transport. Also, the machine settings can be easily adjusted to handle different load sizes and types, offering flexibility while maintaining consistent results.
2. Improved Safety for Workers
Automating the wrapping process minimises the risk of injury caused by repetitive manual tasks. Workers no longer have to bend, twist, or strain themselves to wrap pallets, reducing physical stress.
3. Sustainability and Environmental Impact
Using less plastic film through efficient wrapping reduces the overall environmental footprint. Additionally, there is the potential to use eco-friendly wrapping materials, further contributing to sustainability efforts and aligning with environmentally conscious business practices.
Conclusion
Orbital pallet wrapping machines offer critical benefits for businesses. They improve load stability by securely wrapping products and reducing material waste using less stretch film. Automation leads to time and labour savings and enhances cost efficiency.
By adopting these machines, businesses can lower costs, improve worker safety, reduce product damage, and support sustainability using less plastic. Investing in orbital pallet wrapping machines is a smart choice for companies seeking to streamline their packaging processes and boost efficiency.
Invest in efficiency with an orbital wrapping machine!
Get your free quote today and see how you can improve efficiency, reduce waste, and enhance product safety. Click below to start your journey!
Get Orbital Wrapper Machine Quotes Now!
FAQ:
-
How does orbital wrapping differ from traditional wrapping?
Orbital wrapping uses a rotating ring to apply film around the pallet horizontally, while traditional wrapping typically applies film vertically from top to bottom.
-
What are the benefits of using an orbital pallet wrapping machine?
Benefits include improved load stability, reduced material waste, faster wrapping speeds, lower labour costs, and enhanced worker safety.
-
Can these machines handle irregularly shaped items?
Yes, orbital wrapping machines are designed to securely wrap irregularly shaped products, ensuring consistent coverage.