Hand pallet jacks are valuable tools in material handling operations, but it is essential to prioritize safety when operating them. By following proper safety guidelines, you can prevent accidents, protect yourself and others, and maintain a safe working environment. In this article, we will provide important safety guidelines for operating hand pallet jacks.
1. Operator Training and Certification
Ensure that operators of hand pallet jacks are properly trained and certified. Proper training should cover:
- Familiarization with the specific model of the hand pallet jack being used.
- Understanding of the controls, including the release lever, steering mechanism, and brake system.
- Knowledge of load handling techniques, weight capacity limitations, and proper positioning of the load on the forks.
- Awareness of potential hazards, such as uneven surfaces, obstacles, and other people in the vicinity.
- Operators should receive thorough training on safe operating procedures and be familiar with the manufacturer's guidelines and recommendations.
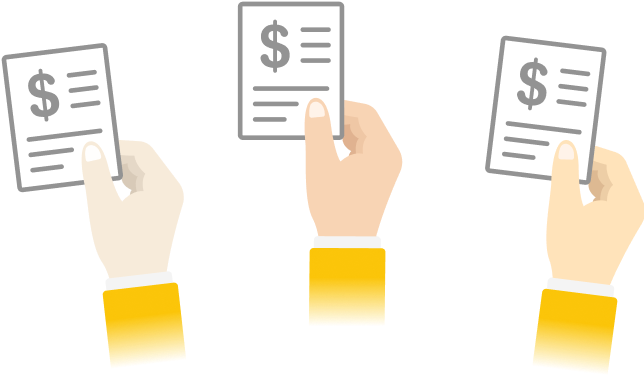
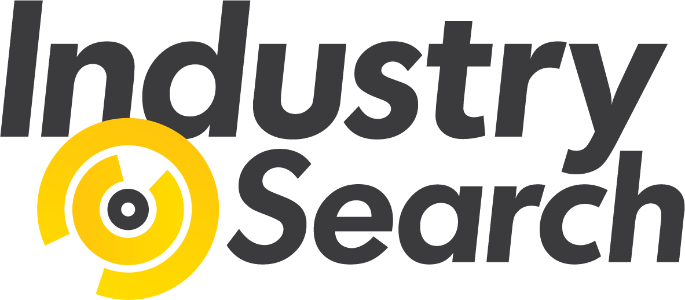
Find the right Hand Pallet Jack
Compare quotes from expert Australian suppliers and make the best choice. It's free, quick and easy!
2. Pre-Operational Inspection
Before using a hand pallet jack, conduct a pre-operational inspection:
- Check for any visible damage or abnormalities, such as bent forks, damaged wheels, or leaking hydraulic fluid.
- Ensure that the release lever, brakes, and steering mechanism are functioning correctly.
- Verify that the load capacity label is clearly visible and legible, providing accurate information about the maximum weight the pallet jack can safely handle.
- If any issues are identified during the inspection, report them to a supervisor or the maintenance department and refrain from using the equipment until repairs are made.
3. Load Capacity and Positioning
Adhere to the load capacity limitations specified by the manufacturer. Overloading the hand pallet jack can compromise stability and pose a safety risk. When positioning the load on the forks:
- Place the load evenly and securely on the forks, ensuring it does not exceed the recommended weight capacity.
- Distribute the weight as evenly as possible to maintain balance during movement.
- Avoid placing the load in a way that obstructs visibility or interferes with the operator's ability to maneuver the hand pallet jack safely.
4. Safe Handling and Operation
Follow these guidelines for safe handling and operation:
- Push, not pull: Push the hand pallet jack from the handle rather than pulling it. This provides better control and reduces the risk of tripping or falling.
- Be aware of surroundings: Watch for obstacles, uneven surfaces, and other people in the vicinity. Use caution when maneuvering in tight spaces or congested areas.
- Use proper lifting techniques: When lifting the forks, keep your back straight and lift with your legs. Avoid twisting your body while carrying a load.
- Control speed: Operate the hand pallet jack at a safe and controlled speed, especially when turning or moving on ramps or inclines.
- Use brakes correctly: Apply the brakes fully when the hand pallet jack is not in use or when loading/unloading. Release the brakes only when ready to move.
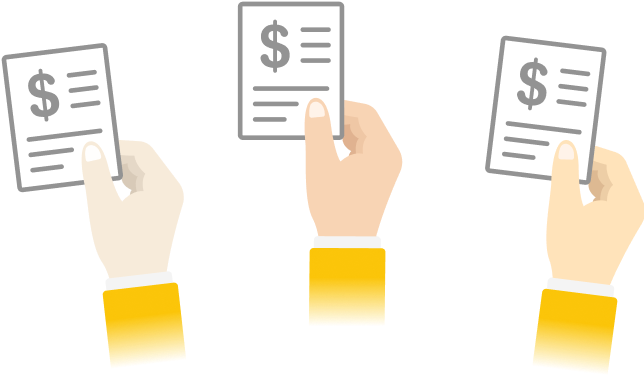
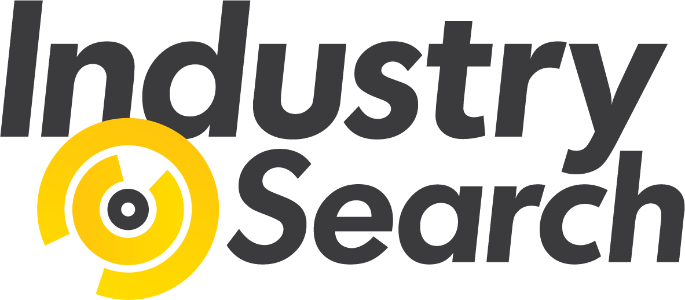
Find the right Hand Pallet Jack
Compare quotes from expert Australian suppliers and make the best choice. It's free, quick and easy!
5. Parking and Storage
When parking or storing a hand pallet jack:
- Place the forks in the lowest position and engage the parking brake.
- Ensure that the hand pallet jack is parked in a designated area away from pedestrian walkways and traffic.
- If possible, secure the equipment with additional measures, such as wheel chocks, to prevent unintended movement.
6. Reporting Incidents and Near Misses
Encourage a culture of safety by reporting any incidents, accidents, or near misses involving hand pallet jacks. This information can help identify areas for improvement, address potential hazards, and prevent future incidents.
Understanding Workplace Safety Regulations for Hand Pallet Jacks
When it comes to the use of hand pallet jacks in different industries, workplace safety regulations and guidelines play a vital role in ensuring the well-being of workers and preventing accidents. Compliance with these regulations is essential to create a safe working environment. In this article, we will provide an overview of relevant safety regulations and guidelines that apply to the use of hand pallet jacks in various industries.
1. Occupational Safety and Health Administration (OSHA)
The Occupational Safety and Health Administration (OSHA) is a regulatory body that sets and enforces safety standards in workplaces in the United States. OSHA provides guidelines for the safe use of hand pallet jacks, including:
- Ensuring that operators are trained and competent in operating the equipment.
- Conducting regular inspections of hand pallet jacks to identify and address any safety issues.
- Following load capacity limitations and proper load handling techniques.
- Implementing proper storage and parking procedures for hand pallet jacks.
- Providing a safe working environment free from hazards, such as obstructions, uneven surfaces, or insufficient lighting.
It is important for employers and employees to familiarize themselves with OSHA regulations specific to their industry and comply with the guidelines to maintain a safe workplace.
2. European Union (EU) Machinery Directive
In the European Union, the Machinery Directive is a key regulation that outlines the essential health and safety requirements for machinery, including hand pallet jacks. The directive focuses on design and manufacturing requirements to ensure the safety of machinery operators and users.
Under the Machinery Directive, manufacturers must adhere to specific safety standards and ensure that hand pallet jacks meet essential requirements such as stability, load capacity labeling, and ergonomic considerations. Employers are responsible for selecting hand pallet jacks that comply with the Machinery Directive and providing proper training and supervision for operators.
3. Industry-Specific Regulations
Various industries may have specific regulations or guidelines that apply to the use of hand pallet jacks. For example:
- In the food industry, regulations may focus on maintaining cleanliness and hygiene standards for hand pallet jacks used in storage areas or refrigerated environments.
- Warehousing and logistics industries may have guidelines related to the safe stacking and handling of palletized loads, as well as traffic management in busy warehouse environments.
- Retail and distribution industries may have regulations specific to the use of hand pallet jacks in customer areas, such as proper maneuvering techniques and pedestrian safety.
Employers and employees should be aware of any industry-specific regulations that pertain to the use of hand pallet jacks and ensure compliance to maintain a safe working environment.
4. Risk Assessments and Safe Work Practices
In addition to regulatory requirements, conducting risk assessments specific to the use of hand pallet jacks is essential. Employers should identify potential hazards and implement appropriate control measures to mitigate risks. This may include:
- Regular inspection and maintenance of hand pallet jacks to identify and address any safety issues promptly.
- Providing comprehensive training and refresher courses for operators to ensure proper handling techniques and awareness of potential hazards.
- Establishing safe work practices, such as maintaining clear pedestrian walkways, using proper lifting techniques, and following designated traffic routes in warehouses or other workplace areas.
By conducting risk assessments and implementing safe work practices, employers can create a safer environment for employees and minimize the risk of accidents.
Personal Protective Equipment (PPE) for Hand Pallet Jack Operators: Ensuring Operator Safety
Personal Protective Equipment (PPE) plays a crucial role in ensuring the safety of hand pallet jack operators. By providing the necessary PPE, employers can protect their employees from potential hazards and reduce the risk of injuries. In this article, we will discuss the essential PPE for hand pallet jack operators to ensure their safety while operating the equipment.
1. Safety Shoes
Safety shoes are a fundamental requirement when operating a hand pallet jack. They provide protection to the feet from various workplace hazards, including:
- Falling objects: Safety shoes with steel toe caps can prevent injuries caused by heavy objects accidentally dropping onto the operator's feet.
- Crushing hazards: The sturdy construction of safety shoes offers resistance against compression, guarding against potential foot injuries caused by heavy loads or equipment.
- Slips and trips: Slip-resistant soles provide better traction on different surfaces, reducing the risk of slips, trips, and falls.
Operators should wear safety shoes that comply with relevant safety standards and provide proper foot support and protection.
2. Gloves
Wearing appropriate gloves is vital for hand pallet jack operators to protect their hands from potential injuries and improve grip and control. Some key benefits of wearing gloves include:
- Hand protection: Gloves act as a barrier against cuts, abrasions, and punctures that may occur during the handling of loads, maneuvering the equipment, or coming into contact with rough surfaces.
- Enhanced grip: Gloves with textured surfaces or coatings enhance grip, enabling better control of the hand pallet jack's handles and reducing the risk of slippage.
- Insulation: In environments with extreme temperatures, insulated gloves can provide protection against cold or heat, ensuring operator comfort and safety.
The type of gloves chosen should be appropriate for the specific tasks and potential hazards involved in operating a hand pallet jack.
3. High-Visibility Vests
High-visibility vests or reflective clothing are crucial for hand pallet jack operators, particularly in environments with vehicle traffic or low-light conditions. High-visibility vests offer the following advantages:
- Increased visibility: Brightly colored vests with reflective strips make operators more visible to others, including forklift operators, pedestrians, and other workers in the vicinity.
- Accident prevention: Enhanced visibility reduces the risk of collisions and accidents, especially in areas with limited visibility or high traffic.
Operators should wear high-visibility vests that meet relevant safety standards to ensure optimal visibility and reduce the likelihood of accidents.
4. Additional PPE
Depending on the specific workplace environment and hazards, additional PPE may be necessary for hand pallet jack operators. This may include:
- Eye protection: Safety glasses or goggles protect against potential eye injuries from flying debris, dust, or chemicals.
- Hearing protection: In noisy environments, such as warehouses or construction sites, hearing protection, such as earplugs or earmuffs, can help prevent hearing damage.
- Head protection: Hard hats or helmets are required in areas where there is a risk of falling objects or head injuries.
Employers should conduct a thorough risk assessment of the workplace to determine the need for additional PPE and ensure that operators are provided with the appropriate protective gear.
Load Securement: Guidelines for Safe Loading and Restraining on a Pallet
Proper load securement on a pallet is crucial for maintaining safety and preventing load shifts or falling objects that could cause injuries. Whether in a warehouse, transportation setting, or any other environment where pallets are used, following guidelines for secure load placement and restraint is essential. In this article, we will provide guidelines to help you securely load and restrain items on a pallet to prevent accidents and injuries.
1. Choose the Right Pallet
Start by selecting an appropriate pallet for the load you are handling. Ensure the pallet is in good condition, without any visible damage or structural defects. Use pallets that are suitable for the weight and dimensions of the load to provide proper support and stability.
2. Proper Load Placement
Follow these guidelines when placing items on a pallet:
- Distribute weight evenly: Ensure the weight is evenly distributed across the pallet to maintain balance and stability. Concentrated or unbalanced loads can increase the risk of tipping or shifting during transport or handling.
- Center the load: Position the load in the center of the pallet to maintain balance and prevent overhang.
- Stack uniformly: Stack items in a stable manner, aligning them neatly on the pallet without any protruding or unsecured edges.
3. Use Palletizing Techniques
Implementing proper palletizing techniques can enhance load stability:
- Interlocking or interweaving: Place items in a way that they interlock or interweave, providing mutual support and reducing the risk of shifting or toppling.
- Layering and interlaying: Utilize layers or interlayers, such as sheets or slip sheets, to separate and stabilize different sections of the load.
- Use load dividers: Consider using load dividers, such as dunnage bags or edge protectors, to create compartments within the load and prevent movement.
4. Restraining Methods
To secure the load on the pallet, employ effective restraining methods:
- Stretch wrap: Use stretch wrap film to tightly wrap the load and secure it to the pallet. Start from the bottom and work your way up, overlapping the wrap for added strength.
- Strapping: Apply sturdy straps or bands around the load and pallet, ensuring they are tight and secure. Use appropriate tension and consider using edge protectors to prevent strap damage to the load.
- Pallet bands or netting: For irregularly shaped or loose loads, consider using pallet bands or netting to contain and secure the items.
5. Consider Transportation Factors
If the loaded pallet will be transported, additional factors should be taken into account:
- Stability during transportation: Consider the mode of transportation (such as trucks or forklifts) and the potential impact of vibrations or movement. Use additional securing methods, such as corner boards or blocking, to enhance stability during transit.
- Clearance and height restrictions: Ensure that the loaded pallet does not exceed height restrictions and can be safely transported through doorways, under low ceilings, or onto transportation vehicles.
6. Inspect and Retighten
Regularly inspect the loaded and secured pallet to ensure everything remains stable and intact. Check for any signs of loosening, shifting, or damage. If necessary, retighten straps or reapply stretch wrap to maintain load security.
Operator Training and Certification in Australia: Ensuring Safe and Efficient Operation of Hand Pallet Jacks
Comprehensive training programs and certification requirements are vital for hand pallet jack operators in Australia to ensure the safe and efficient operation of this equipment. Training programs provide operators with the necessary knowledge and skills to handle hand pallet jacks correctly, minimizing the risk of accidents and injuries. In this article, we will discuss the importance of providing comprehensive training programs and certification requirements for hand pallet jack operators in Australia.
1. Ensuring Operator Safety
Comprehensive training programs prioritize operator safety by covering essential aspects such as:
- Equipment familiarity: Training programs familiarize operators with the specific model of hand pallet jack they will be using. This includes understanding the controls, features, and limitations of the equipment.
- Proper handling techniques: Operators learn the correct techniques for maneuvering, lifting, and placing loads on pallets using hand pallet jacks. This includes understanding load capacity, weight distribution, and load stability.
- Hazard identification and risk assessment: Operators are trained to identify potential hazards in the workplace and assess associated risks. This empowers them to take proactive measures to mitigate risks and prevent accidents.
- Safe operating procedures: Training programs outline safe operating procedures, including guidelines for starting and stopping the equipment, turning, navigating obstacles, and operating in confined spaces.
- Emergency response: Operators are educated on emergency procedures, such as what to do in the event of equipment malfunctions, power failures, or other unexpected situations.
- Workplace safety regulations: Training programs provide operators with knowledge of relevant workplace safety regulations, ensuring compliance and creating a safer working environment.
Comprehensive training programs equip operators with the necessary skills and knowledge to operate hand pallet jacks safely and effectively.
2. Increasing Operational Efficiency
Training programs enhance operational efficiency by improving operator skills and efficiency in using hand pallet jacks. This includes:
- Time-saving techniques: Operators learn efficient techniques for loading, unloading, and maneuvering loads using hand pallet jacks, reducing operational downtime and increasing productivity.
- Optimal equipment utilization: Training programs educate operators on maximizing the capabilities of hand pallet jacks, including understanding load capacity, ergonomic positioning, and efficient use of controls.
- Preventative maintenance awareness: Operators gain knowledge about basic maintenance tasks and the importance of regular equipment inspections. This helps identify and address potential issues before they lead to equipment failure or accidents, minimizing downtime and maintenance costs.
By providing comprehensive training, employers can improve operational efficiency and ensure hand pallet jacks are used effectively and optimally.
3. Compliance with Regulations and Standards
In Australia, certain regulations and standards govern the operation of hand pallet jacks. By incorporating certification requirements into training programs, employers ensure compliance with these regulations. Certification provides evidence that operators have successfully completed the necessary training and possess the required skills and knowledge to operate hand pallet jacks safely.
Certification requirements may vary depending on the specific state or territory in Australia. It is important for employers to understand and adhere to the certification requirements applicable in their jurisdiction to ensure legal compliance and create a safer workplace.
4. Fostering a Safety Culture
Comprehensive training programs and certification requirements promote a safety culture within the workplace. When operators receive thorough training and certification, they become more conscious of safety practices and actively contribute to maintaining a safe working environment. This can lead to improved overall safety performance, increased employee morale, and reduced accidents and injuries.
In conclusion, following safety guidelines for hand pallet jacks is crucial to ensure safe operations. This includes operator training, pre-operational inspections, proper load capacity and positioning, safe handling and operation practices, reporting incidents and near misses, complying with workplace safety regulations, using appropriate personal protective equipment (PPE), and providing comprehensive training programs and certification requirements. Prioritizing safety through these measures helps protect operators and maintain a safe working environment.