Robotic palletisers have revolutionized the field of industrial automation, offering businesses increased efficiency and productivity in their palletizing operations. In this comprehensive buying guide, we will explore the key factors to consider before purchasing a robotic palletiser in Sydney, the benefits they offer, the different types available in the market, and popular brands to help you make an informed decision.
What is a Robotic Palletiser?
A robotic palletiser is an automated system designed to stack and arrange goods onto pallets. It uses robotic arms equipped with grippers to lift, position, and stack products, replacing the traditional manual palletizing process. These intelligent machines can handle a wide range of products, including boxes, bags, cases, and cartons, with precision and speed.
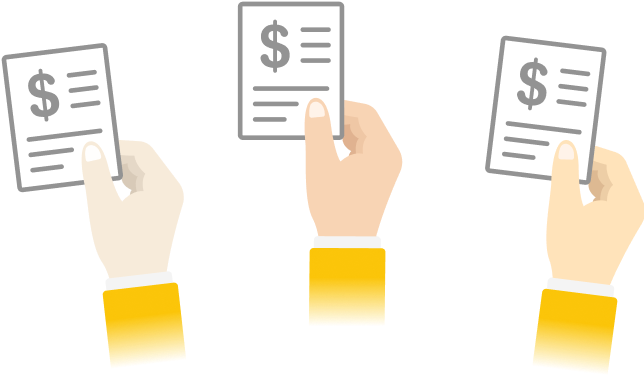
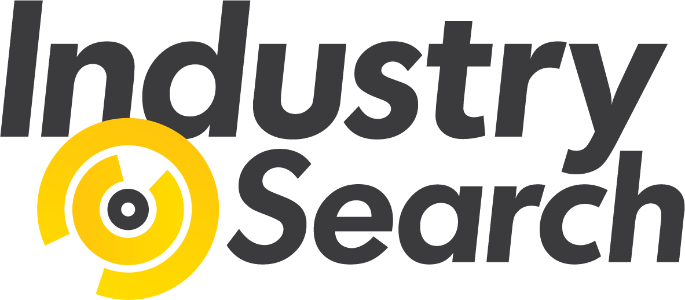
Find the right Robotic Palletising System
Compare quotes from expert Australian suppliers and make the best choice. It's free, quick and easy!
Benefits of Robotic Palletisers
Robotic palletisers offer several benefits over manual palletizing methods. Here are some key advantages:
a. Increased Efficiency
Robotic palletisers can stack products at a much faster rate compared to manual labour. With their precise movements and optimized stacking algorithms, these machines can significantly improve operational efficiency and throughput. This increased efficiency translates into shorter production cycles and faster order fulfilment.
b. Improved Workplace Safety
By automating the palletizing process, businesses can eliminate the risks associated with manual labour, such as lifting injuries and musculoskeletal disorders. Robotic palletisers provide a safer working environment by taking over repetitive and physically demanding tasks, reducing the likelihood of accidents and injuries.
c. Enhanced Product Quality
Robotic palletisers ensure consistent and accurate stacking, resulting in neatly arranged pallets that are less prone to product damage during transportation. This helps businesses maintain product quality and reduce losses due to damaged goods.
d. Flexibility and Versatility
Modern robotic palletisers are designed to handle a wide range of product types, shapes, and sizes. By incorporating adjustable grippers and end-of-arm tools, these machines can adapt to different packaging configurations, making them suitable for diverse industries and applications.
e. Scalability and Adaptability
Robotic palletisers can be easily integrated into existing production lines and can be scaled up or down to meet changing business needs. They offer the flexibility to handle increased production volumes without significant investments in additional labour or equipment.
5 Types of Robotic Palletisers
Robotic palletisers come in various types, each designed to cater to different needs and requirements in factories and warehouses. Let's explore some of the common types of robotic palletisers and their functionalities:
1. Cartesian Robotic Palletisers
Cartesian robotic palletisers, also known as gantry palletisers, are widely used in industries where high-speed palletizing is required. These machines consist of an overhead gantry system with multiple axes of movement. Cartesian palletisers are known for their exceptional speed, precision, and versatility in handling different product sizes and shapes.
2. Articulated Robotic Palletisers
Articulated robotic palletisers, also referred to as robotic arms, mimic the flexibility and movement range of human arms. These palletisers are made up of multiple joints, allowing them to handle products from various angles and positions. Articulated palletisers are highly adaptable and are ideal for applications that involve complex palletizing patterns or irregularly shaped products.
3. Collaborative Robotic Palletisers
Collaborative robotic palletisers, also known as cobots, are designed to work alongside human workers in a shared workspace. These palletisers are equipped with advanced sensors and safety features to ensure the safety of human operators. Collaborative palletisers offer the advantage of increased flexibility and efficiency by combining the strength and precision of robots with the decision-making capabilities of human workers.
4. Mobile Robotic Palletisers
Mobile robotic palletisers are a recent innovation that allows the palletising process to be taken directly to the products, rather than transporting products to a fixed palletising station. These machines are equipped with autonomous navigation systems, enabling them to move freely within the facility and adapt to changing layouts or product locations. Mobile palletisers offer increased agility and efficiency, particularly in large warehouses or facilities with frequently changing inventory.
5. Layer Robotic Palletisers
Layer robotic palletisers are specialized machines designed to handle palletizing tasks at the layer level. Instead of stacking individual products, these palletisers can pick up entire layers of products from conveyors or pallet magazines and place them on pallets. Layer palletisers are commonly used in industries where the packaging of products is done in pre-defined layers, such as cases of beverages or cartons of packaged goods.
Key Considerations for Industry Professionals When Purchasing a Robotic Palletiser
As an industry professional well-versed in the realm of material handling operations, you understand the importance of selecting the right robotic palletiser to optimize your processes. However, as new information emerges in this dynamic field, it's essential to stay informed and enrich your decision-making process. Here are key considerations, further expanded to reflect the latest advancements and insights:
-
Payload Capacity: Maximizing Efficiency and Safety
The payload capacity of a robotic palletiser continues to be a vital factor in your decision-making process. It is imperative to accurately assess the weight and dimensions of the products you intend to palletise. Furthermore, consider how advancements in technology have improved palletizers load-bearing capabilities. With innovations in materials and designs, you can now find palletisers that offer enhanced strength without compromising efficiency or safety. By incorporating these advancements into your assessment, you can ensure that the palletiser you choose aligns perfectly with your specific payload requirements.
-
Speed and Efficiency: Pushing the Boundaries
In an ever-evolving industry, the need for speed and efficiency remains paramount. As an industry professional, you understand the importance of evaluating your desired production rate and throughput requirements. However, recent developments have revolutionized the capabilities of palletisers in terms of speed and efficiency. State-of-the-art robotic palletisers now feature advanced algorithms and optimized motion control systems, enabling them to stack products at unprecedented speeds while maintaining exceptional precision. By exploring these cutting-edge options, you can elevate your operational capabilities and achieve unparalleled productivity gains.
-
Flexibility and Versatility: Adapting to Dynamic Needs
In today's fast-paced environment, adaptability is key. As an industry professional, you are familiar with the challenge of handling various product types, sizes, and configurations. While considering a palletiser's flexibility and versatility, it's crucial to delve deeper into the latest advancements in gripper technology. Adjustable grippers with intuitive sensing capabilities, coupled with end-of-arm tools that can be easily swapped out, allow for seamless transitions between different products. Additionally, exploring the latest developments in customizable programming capabilities enables you to adapt to changing needs efficiently and effectively.
-
Integration Ease: Streamlining Your Operations
Ensuring seamless integration of a robotic palletiser into your existing production line continues to be a critical factor for industry professionals. In today's interconnected world, advancements in communication protocols and compatibility standards have simplified integration processes. Furthermore, manufacturers and suppliers now offer comprehensive support packages that encompass everything from initial setup to ongoing technical assistance. By leveraging these advancements, you can streamline your operations, reduce downtime, and ensure a smooth transition to your new palletiser.
-
Safety Features: Advancing Operator Protection
Safety is a top priority in any industrial setting, and recent developments in robotic palletisers have further strengthened operator protection. Beyond the traditional safety features such as collision detection and emergency stop buttons, palletisers now incorporate sophisticated sensors and advanced artificial intelligence algorithms. These advancements enable real-time monitoring of the operating environment, minimizing the risk of accidents and optimizing the overall safety of your operations. Prioritizing these cutting-edge safety features demonstrates your commitment to providing a secure working environment for your team.
-
Maintenance and Support: Maximizing Longevity and Performance
As an industry professional, you recognize that regular maintenance and robust support are crucial for ensuring the longevity and optimal performance of your palletiser. In recent years, manufacturers and suppliers have taken significant strides in providing comprehensive maintenance programs and technical support. They offer proactive monitoring systems that identify potential issues before they escalate, ensuring minimal downtime and maximum productivity. Furthermore, training programs have evolved to encompass not only initial setup but also ongoing skill development for your team members. By leveraging these advancements in maintenance and support, you can ensure that your palletiser operates at peak performance throughout its
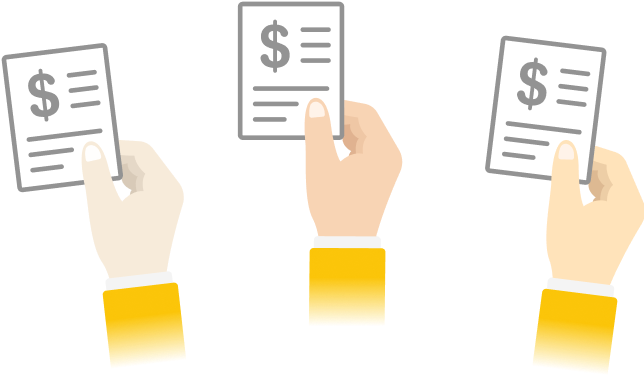
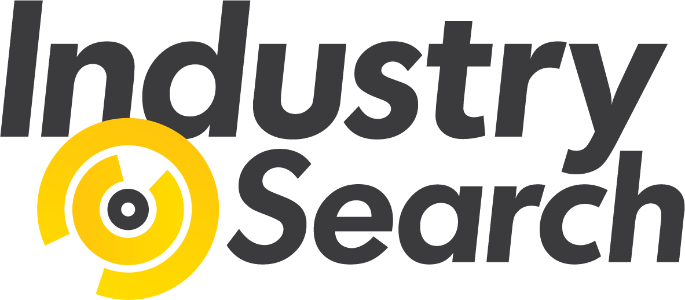
Find the right Robotic Palletising System
Compare quotes from expert Australian suppliers and make the best choice. It's free, quick and easy!
Robotic Palletisers: New vs. Used – Which is the Best Option?
When it comes to purchasing a product, one common dilemma that consumers often face is whether to buy something new or used. This debate is particularly relevant when it comes to larger investments like cars, electronics, and even homes. Both options have their own advantages and disadvantages, making it essential for buyers to consider their individual needs and circumstances.
Buying new offers the allure of having the latest technology, untouched by previous owners, and often comes with warranties and guarantees. On the other hand, buying used can provide significant cost savings and the potential to find unique or vintage items that are no longer available in the market. Each option presents a different set of considerations, and understanding them can help individuals make the best decision for their specific situation.
The Benefits of New Robotic Palletisers
Investing in a new robotic palletiser comes with a range of advantages that make it an attractive option for many businesses. Here are some key benefits:
1. Cutting-Edge Technology
New robotic palletisers incorporate the latest technological advancements. Manufacturers are constantly innovating to improve the efficiency, speed, and capabilities of these machines. Investing in a new system allows you to leverage cutting-edge features and stay at the forefront of palletizing technology.
2. Customization and Scalability
New palletising systems can be tailored to meet your specific requirements. Manufacturers offer customization options, allowing you to configure the machine according to your production line needs. Additionally, new systems are scalable, accommodating future growth and expanding production demands.
3. Warranty and Support
When you purchase a new robotic palletiser, you typically receive a warranty and ongoing support from the manufacturer. This provides peace of mind and ensures that any technical issues or maintenance needs will be promptly addressed.
4. Energy Efficiency
Modern robotic palletisers are designed to be energy-efficient, helping you reduce your carbon footprint and operational costs. These systems often incorporate features such as energy recovery mechanisms and optimized motor control, resulting in significant energy savings over time.
The Advantages of Used Robotic Palletisers
While new robotic palletisers offer a range of benefits, opting for a used system can also be a viable option for certain businesses. Let's explore some advantages of choosing a used palletising system:
1. Cost Savings
One of the most significant advantages of purchasing a used robotic palletiser is cost savings. Used systems are generally more affordable than new ones, making them an attractive option for businesses with budget constraints. By investing in a used palletiser, you can allocate your resources to other areas of your operations.
2. Availability
The used machinery market offers a wide selection of robotic palletisers from different manufacturers and models. This abundance of options gives you the flexibility to find a system that matches your requirements and production specifications.
3. Immediate Availability
Unlike new systems that might have a lead time for manufacturing and delivery, used robotic palletisers are readily available. This allows you to implement the solution quickly and minimize any disruption to your production schedule.
4. Proven Performance
Used robotic palletisers often come with a track record of performance. You can gather information on the machine's previous usage, maintenance history, and productivity levels before making a purchase. This can provide reassurance that the used system has proven reliability and can effectively meet your palletizing needs.
In summary, this comprehensive buying guide provides industry professionals with a wealth of information and insights into the world of robotic palletisers. By understanding the benefits, types, and key considerations associated with these automated systems, businesses can make informed decisions that align with their specific needs and requirements. The guide emphasizes the importance of factors such as payload capacity, speed and efficiency, flexibility and versatility, integration ease, safety features, and maintenance and support. It also explores the advantages of both new and used robotic palletisers, allowing businesses to weigh the benefits of cutting-edge technology and customization options against cost savings and immediate availability. By leveraging the knowledge and recommendations presented in this guide, industry professionals can enhance their material handling operations, streamline processes, and achieve higher levels of efficiency, productivity, and overall success.